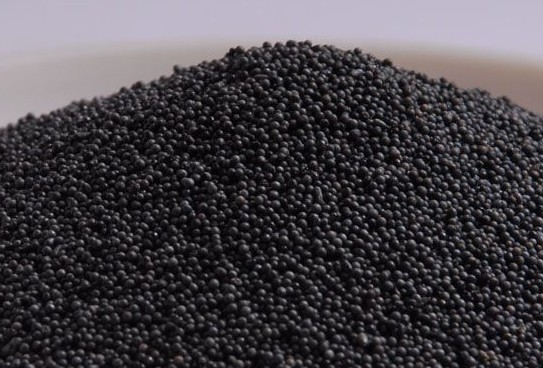
定义:
中文名称:宝珠砂
英文名称:ceramsite
宝珠砂又名铸宝砂(NFS CERAMSITE = Nice Foundry Sand)是对熔融状态下的高氧化铝质的原料(铝矾土喷砂磨料)进行喷雾处理,使之再结晶而得到的高耐热性,低热膨胀,球状人工铸造砂。
产品简介:
宝珠砂又名电熔陶粒,是石英砂的高级替代品。
石英砂的优点是分布广泛,成本低廉;但其缺点也相当明显:一是膨胀系数大,铸件精度低;二是铸件表面粘砂严重,清砂困难。究其因,是石英在不同的温度下会有多种同质异晶体生成,体积变化大;受耐火度 ( 石英砂的耐火度在 1400 -1700 ℃ 之间 ) 的限制,铸件局部(孔、槽、及热节集中的部位)粘砂严重,清理十分困难。上述缺点在大型铸钢件的生产中尤为严重。
宝珠砂 |
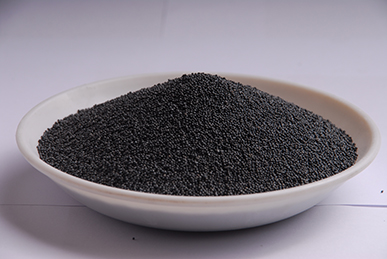 |
宝珠砂能克服这些缺点,从而大大提高了铸件的质量。
宝珠砂是对熔融状态下的高氧化铝质的原料(铝矾土喷砂磨料)进行喷雾处理,使之再结晶而得到的高耐热性,低热膨胀,球状人工铸造砂。结构致密,粒型极似球形,表面光滑且表面积小。具有耐高温、良好的透气性、溃散性、抗酸碱侵蚀性、破碎率低等优点,性价比由于铬铁矿砂、锆英砂,为铸造厂家提高铸件质量,降低生产成本和减少环境污染提供了简便并有效的方法。铸宝砂是目前公认最理想的新型铸造用砂,具有非常广阔的发展前景。
虽然宝珠砂的价格比硅砂高不少,如使用得当,全面核算下来,不仅可明显提高铸件质量,而且可降低生产成本
1、宝珠砂的耐火度高于硅砂,而且造型时填充的紧实度高,因而,可使铸件的表面质量提高,生产中的废品率降低;
2、球形的宝珠砂流动性很好,对于形状复杂的铸件,内夹角、深凹处、平孔等难以填充的部位,都易于填紧。因而,可显著减少这些部位的包砂缺陷,大幅度减少清理和精整的工作量;
3、耐破碎性好, 回收率高,排放的废弃物也相应地减少;
4、热膨胀率小,热稳定性好,不会发生二次相变而引起膨胀缺陷,大大提高了尺寸精度
5、消失模实型铸造,树脂的用量可减少约1/3
物理指标:
宝珠砂的物理及化学性能
粒 形 |
球形 |
|
膨胀系数 |
(20-1000 ℃) 6 × 10-6/℃ |
颜 色 |
黑棕色 |
|
粒度 |
6-320 目(φ0.053-3.36mm) |
耐火温度 |
≥ 1900 ℃ |
|
Al2O3 |
75-85% |
堆积比重 |
1.95 -2.05g /cm |
|
SiO2 |
≤ 15% |
真 密 度 |
2.9g /cm |
|
TiO2 |
≤ 1.5% |
热 导 率 |
(1200 ℃)5.27W/M·K |
|
PH 值 |
7 - 8 |
化学指标:
主要化学组成(代表值)
成分
|
Al2O3
|
SiO2
|
Fe2O3
|
TiO2
|
CaO
|
MgO
|
K2O
|
Na2O
|
%
|
75.36
|
17.72
|
2.16
|
3.23
|
0.43
|
0.35
|
0.33
|
0.08
|
宝珠砂 - 宝珠砂与铬铁矿砂、锆英砂主要性能比较
堆密度(g/㎝)
|
1.95-2.05
|
2.9-3.1
|
2.6-2.7
|
真密度(g/㎝)
|
2.9
|
4.4-4.71
|
3.9-4.8
|
粘结剂加入量(水玻璃 +CO2硬化)
|
3-4%
|
7-8%
|
7-8%
|
使用范围(用途):
目前,宝珠砂广泛应用于树脂砂(呋喃树脂、酚醛树脂),水玻璃砂(有机脂、 CO 2 硬化),覆膜砂。适于各种金属铸件:如:碳钢、合金钢(高锰钢、高铬铸铁),铸铁、铸铜等。
宝珠砂是一种非石英质型人造砂,适用于各种铸造方式;如: V 法, VRH ,消失模,熔模,一般砂型(粘土砂、水玻璃+ CO 2 硬化)、树脂砂等;适用于各种粘结剂、各种金属材料的铸件生产,不但能大幅度提高铸件质量,而且清砂容易,配砂工艺简单方便(大型铸钢厂单件小批量局部用砂,少量用砂人工混制即可),对大多数铸件可以省去涂料,尤其适宜制作质量要求高的铸件。
值得注意的是:在使用水玻璃 CO 2 硬化砂中,吹干的芯、型,不宜再上窑烘干(如烘干一定要控制加热速度)。随着铸造业的发展和社会环保的要求,局部和全部使用宝珠砂的厂家会越来越多,它已被誉为环保型( GREEN BEADS )铸造材料,有很好的推广使用前景。
应用范围广
水玻璃砂、树脂砂、精密铸造及铜、铝件的抛光清理
应用领域
Ⅰ 用于V-法铸造和消失模铸造
V 法铸造全部用干砂造型,消失模铸造大部分也采用干砂造型。如采用硅砂,落砂过程中散发硅粉尘很多,劳动条件很坏,这是亟待解决的问题。用宝珠砂代替硅砂,可大幅度减少散发的粉尘,而且粉尘中所含的硅质粉尘很少,对改善劳动条件和保护环境意义重大。
除此以外,还有以下好处:
1、宝珠砂的耐火度高于硅砂,而且造型时填充的紧实度高,因而,可使铸件的表面质量提高,生产中的废品率降低;
2、球形的宝珠砂流动性很好,对于形状复杂的铸件,内夹角、深凹处、平孔等难以填充的部位,都易于填紧。因而,可显著减少这些部位的包砂缺陷,大幅度减少清理和精整的工作量;
3、每吨铸件耗用的型砂量可减少90%,排放的废弃物也相应地减少;
4、消失模铸造采用树脂粘结砂造型时,树脂的用量可减少1/3。
虽然宝珠砂的价格比硅砂高不少,如使用得当,全面核算下来,不仅可明显提高铸件质量,而且可降低生产成本。
宝珠砂的热膨胀率低是一项重要的优点,可防止铸件产生膨胀缺陷,但这一特性也有一定的负面作用。由于其受热后的膨胀率比硅砂低得多,生产铸铁件,特别是球墨铸铁件时,铸型制约铸件石墨化膨胀的作用较差,因而铸件易产生收缩缺陷,应适当地设置冒口。
Ⅱ 在熔模铸造中替代锆砂和锆砂粉
目前,我国熔模精密铸件的年产量在50万吨以上,型壳废料大约在100万吨以上,型壳材料的循环利用,是一项值得关注的重要课题。
质量较高的熔模精密铸件,型壳的面层耐火材料(包括涂料中的骨料和撒砂)大都采用锆砂粉和锆砂。铸件脱壳后,无法将其与背层耐火材料分离,不仅浪费了资源短缺、价格高昂的锆砂,而且增加了型壳废料回收利用的难度。
从1996年底开始,日本就将提高熔模铸造技术、开发型壳面层用人造材料,列为战略性基础技术研发课题之一,由日本铸造协会管理,日立金属、ヨネダアドキャスト、キングパ-ツ、キャステム、妙中矿业等知名铸造企业,以及伊藤忠陶瓷联合实施,这一课题于2009年11月完成。主要成果是用烧结陶粒代替锆砂,用陶粒粉代替锆砂粉,背层则仍然采用与陶粒成分相近的硅铝质耐火材料。
这种型壳可用于大气铸造和真空铸造,已用以制成燃气轮机的镍基合金喷嘴环。为了保证面层涂料中骨料的填充性能,面层涂料所用的陶粒粉予以表面烧熔处理。处理方法是:粉料通过高温火炎,使其棱角烧熔、表面光滑。
由于型壳所用的耐火材料全部是硅铝质材料,废弃的型壳,全部由伊藤忠陶瓷公司回收,经适当处理后,重新制成陶粒和陶粒粉,循环利用,既节省了锆砂,又保护了资源。
我国的宝珠砂,是经电熔后制得的,质地致密,表面光滑,性能优于烧结陶粒。特别应该提到的是:制造宝珠砂时,由于喷吹的作用,270目以下的微粒(粒径0.053㎜以下)可能有5%左右。这些微粒,保留在宝珠砂中是不适宜的。如果将其收集,用于配制面层涂料,填充性能一定明显优于经表面熔烧处理的粉料。
因此,可以认为:目前,我国熔模铸造行业中免用锆砂的条件已经具备。
Ⅲ 在生产中、大型铸钢件方面替代铬铁矿砂
宝珠砂,除堆密度低于铬铁矿砂以外,一些主要的热物性,如热导率、热膨胀率、耐火度等,都与铬铁矿砂相近。在颗粒形状和耐破碎性方面,则比铬铁矿砂好得多,而价格却只是铬铁矿砂的1/2左右。在综合分析的基础上,不难看出,宝珠砂是铬铁矿砂比较理想的替代材料。
日本特殊制钢所已在生产中采用烧结陶粒代替铬铁矿砂,效果不错,不足之处是铸件表面易产生粘砂缺陷。通过试验研究,得到的解决方案是加入4%的球状氧化铁。
宝珠砂的表面状况远优于烧结陶粒,铸件应该不易于产生粘砂缺陷。实际上,我国已有几家铸钢厂用宝珠砂替代铬铁矿砂,都得到了很好的效果。用宝珠砂代替铬铁矿砂,既能提高铸件的表面质量,又可降低生产成本,而且还便于旧砂的再生、回用。
Ⅳ 在树脂粘结砂和粘土湿型砂中代替硅砂
在型砂、芯砂中配用部分宝珠砂,能有效地防止铸件产生膨胀缺陷。
近年来,我国一些覆膜砂制造厂商,已在原料砂中配加部分宝珠砂,从而可以使制成的壳型、壳芯具有耐高温、低膨胀、易溃散、高强度、发气量低等性能。对于形状特别复杂的芯子,还可以解决射砂不易紧实的问题。
为适应轻量化的要求、生产薄壁铸铁件时,如面砂中配入部分低密度陶粒,可有效地解决浇不足和冷隔之类的问题,而且可避免铸件出现或过冷组织。这方面国外已有成功的经验,我国尚未见相关的报道。
在造型方面,用宝珠砂代替硅砂,有以下优点:
1、工作场所大气中粉尘含量大幅度减少,特别是其中的硅质粉尘很少,这一点今后将越来越成为人们关注的焦点;
2、 每吨铸件的原砂耗用量可大幅度减少,节省资源;
3、由于砂粒的流动性好,在相同的紧实条件下,铸型、芯子的紧实度提高,而且仍保持良好的透气性,有助于提高铸件质量;
4、型砂的起模性能显著改善,可减小模样的起模斜度,减少起模时的掉砂,有助于提高铸件的尺寸精度和表面质量;
目前,宝珠砂的价格比硅砂高得多,虽然其耗用量减少,仅就型砂而言,用人造砂代替硅砂,成本仍然较。但是,如果作全面的考核,总体效益可能会优于采用硅砂。
用宝珠砂代替硅砂有很多好处,但是,一种新材料的应用,一定也会有一些问题,需要认真地认识和了解,并采取恰如其分的措施,如:
(1)铸铁件的缩孔、缩松倾向
生产铸铁件,特别是球墨铸铁件时,虽然铸型的紧实度较高,型壁运动量小,有减少缩孔倾向的作用,但是,宝珠砂的热膨胀率只是硅砂的1/10,几乎没有硅砂膨胀对铸件石墨化膨胀的抑制作用,铸件产生缩孔、缩松的倾向增大。在多数情况下,后一因素的作用大于前一因素,铸件就可能出现缩孔、缩松类缺陷。
改变原砂时,工艺设计人员,应该通过试验,正确掌握所用型砂的特性,适当地设置冒口和冷铁。
(2)因比热容大而影响树脂自硬砂的硬化
酸硬化的呋喃树脂树脂自硬砂、甲阶酚醛树脂自硬砂,树脂的硬化是缩合反应,也就是说,树脂发生交联反应、硬化时,要析出水,需要热量使水分蒸发、逸出,反应才能继续进行。人造砂的比热容都比较大,特别熔制莫来石砂(宝珠砂),其比热容几乎是硅砂的2倍。树脂发生硬化反应时,如果砂粒过多地吸收了树脂硬化反应所析出的热量,就会影响型砂的硬化速度和初始强度。由于还有其他影响因素的作用,也有的铸造厂,在采用宝珠配制呋喃树脂自硬砂时,未发现这种情况。但是,对这一问题必须予以认真的观察和分析。
现阶段,国内一些知名的宝珠砂生产企业及覆膜砂生产企业已经可以成熟的应对和避免此问题。如盛达宝珠砂等企业。
V 在钢包引流剂方面,代替铬铁矿砂
现如今钢包引流剂的主要品种有硅砂引流剂、铬铁矿砂引流剂。而硅砂引流剂不利于填砂的自由下落,自然流动性差,易引起棚料;铬铁矿砂引流剂的性能很好,但对环境污染严重,成本高。
而宝珠砂引流剂是铬铁矿砂比较理想的替代材料,并且其粒形为球形,可有效降低烧结层的强度,有利于引流砂开浇;另外其比重小,成本远远低于铬铁矿砂。
在生产引流砂方面,宝珠砂代替铬铁矿砂有以下优势:
1、球状粒形:粒形接近真圆,表面光滑,无凹凸脉纹,其流动性好,利于开浇;
2、热膨胀率低:具有低热导率,受热后膨胀小,可防止棚料
3、耐火度高:主要成分是三氧化二铝,所以耐火度≥1790℃,在一定的钢水温度下不过度烧结,可减少烧结层的厚度
4、与钢水接触可形成均与保护层,利用阻止引流少上浮,钢水渗透
5、因宝珠砂为圆形,烧结层颗粒之间为点接触,能有效地降低烧结层的强度,使引流砂利用开浇
6、在引流砂中,按配比可全部用宝珠砂,也可部分宝珠砂替代铬铁矿砂,价格远远低于铬铁矿砂
使用时要注意,加入的引流剂要堆积成小包型,包型的中心要与钢包出水口对正。 出钢时要防止钢流直接冲击包型而影响开浇自流率。
二.铸宝砂铸造陶粒具有如下优点
1. 球状粒形
粒形接近真圆,表面光滑,无凹凸脉纹。其流动性及填充性好,能得到良好的成型性和铸模强度。溃散性好,易于清砂作业。粘结剂使用量较其他同类型砂有较大的节省。
2. 热膨胀率低
热膨胀率之低于铬矿砂等特殊砂相同,所以,生产铸件的尺寸精度高,破裂及表面缺陷少,铸件成品率高。
3. 耐破碎性好
铸宝砂的致密性好,强度高,即使重复再生使用也很少破碎,减少铸造生产过程中的粉尘对生产环境的污染,再生性好,减少产业废物排放,利于环境保护。
4. 耐火性好
主要成分是氧化铝,所以耐火性能很好。耐火度≥1790℃能满足铸造各种金属及合金。
相关介绍:
历史沿革
我国洛阳一带,高铝矾土喷砂磨料资源丰富,十多年前就由生产企业与高等学校合作研制莫来石质人造砂,由盛达宝珠砂、洛阳宝珠砂公司等企业生产,这种产品最初的名称为“宝珠砂”,后来盛达宝珠砂又称之为“铸宝砂”,实际上都是相同的产品。
“宝珠砂”具有多种优异的性能,可适用于各种铸造合金和多种铸造工艺,而价格低于锆砂和铬铁矿砂。“宝珠砂”问世之初,很快就受到了外国铸造行业的重视,早期的产品主要出口到日本,并由日本转销到其他国家。近几年,我国铸造行业中也已开始采用,并取得了很好的效果。
目前,我国宝珠砂的年产量约在10万吨以上,早期,大部分都出口供外国使用,国内应用不多,近几年,国内的用量虽逐渐有所增加,但仍然未能充分利用我们自己的优势。今后,我国铸造行业应该特别关注宝珠砂的推广、应用。
宝珠砂与锆英砂相比存在以下优势:
1、宝珠砂粒型极似球形,粘结剂使用量少
2、相对于资源紧缺价格昂贵的锆英砂,其原料储藏丰富,价格低廉。
3、其耐破损性好,回收率高,可循环利用,既节约了锆砂又保护了环境,避免了锆英砂的放射性对一线工人的伤害
英文说明:
Henan Ruishi Investment Group Co., Ltd. ( Ceramic Foundry Sand Branch Plant) professionally produce Ceramic Foundry Sand, Ceramic Foundry Sand also named ( Ceracite, Fused Ceramic, Ceramic Sand), Ceramic Foundry Sand is fused in the electric Furnace with high quality bauxite as the raw material, our Capacity is 18000MT per year. Ceramic Foundry Sand is widely used in various casting ways ( investment casting, full mold casting, lost foam casting and so on ); Ceramic Foundry Sand is the new type casting sand used in precision casting, resin coated sand, self-hardening sand. And also can be used for shot peening( aluminum, copper, steel casting).Ceramic Foundry Sand with reasonalbe price, Ceramic Foundry Sand has advantage of cost and performance than chromite sand and zircon sand; especially low expansion, unsintered , non pulverise , non craze
Non stick (Eliminate the negative infection on the quality of casting ), regeneration performance good, and increase the production yield of casting.
The specification of Ceramic Foundry Sand:
Chemical Composition% |
Physical composition |
Al203 |
Fe203 |
Ti02 |
Si02 |
Shape:ball shape
Refractory Degree:1790℃
Size: 5-320目( 0.053mm-2.0mm)
Density( Bulk density) 1.96-2.05(g/cm3)
Thermal expansion : 0.13%(10 minutes at 1000℃)
|
70-80 |
≤5 |
2.5-3.5 |
8-20 |